|
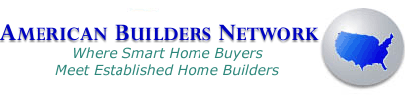
Home
Building Resources
| Home
Prefab is Not The Answer to
Affordable, Modern & Green Homes
by Chad Ludeman
Prefab homes seem to be showing
up more and more in the media these days, especially with two
large exhibits in Philadelphia showcasing their history this
year. Like many, I hoped that prefab would be the answer to
bringing modern architecture to the masses in the US and
beyond. I thought that finally, modern home design would be
attainable by those of us who aren't pulling in lofty six figure
incomes. That was until I conducted extensive research into the
possibility of starting a development company in Philadelphia
using only prefab homes.
Don't get me wrong, I love prefab and many of the firms out
there with cutting
edge designs in the prefab realm. There are also a variety
of building lessons that can be learned from the prefab
methodology. I just don't believe it is the best way of
delivering modern design to the average new home buyer.
Below we will look at this issue from two points of view.
First, we will look at the prefab industry and try to dispel
some of the myths that have arisen around it. Second, we will
take a quick look at how the housing industry may be able to
learn from both prefab and site-built homes to create a hybrid
approach that will provide a better, more accessible solution to
the home buyer and hopefully reduce the barrier of entry to
modern, green, and unique residences.
Names and firms have intentionally been left out of this post in
an effort to discuss only the facts, dispel some of the myths of
prefab, and possibly look towards a better method for bringing
modern homes to the average American.
Prefab's Claims to Greatness
There are a variety of claims
made by prefab proponents to support the idea that this method
of home delivery is the best way to provide modern architecture
to the masses. Not every prefab supporter or manufacturer makes
every one of these claims, but they are pervasive enough that we
will address them as the claims of the industry as a whole.
They are:
- Prefab is more Affordable
- Prefab produces less Waste
- Prefab takes less Time
- Prefab is more "Green"
OK, let's look at each of these "myths of prefab" one by one.
More Affordable. We are starting here because it is the
easiest to disprove, and is also the main reason that many start
looking into prefab. Unfortunately, most find, after weeks of
research, that they just cannot afford any modern prefab unit on
the market today. This just doesn't seem fair.
The bottom line is that most modern prefabs today that someone
interested in modern architecture would consider buying will
cost at least $250 per square foot when all is said and done.
This includes everything but the land cost which can vary
greatly based on the buyers location. There are a few people
out there that claim to get very close to $200 psf, but there
are many more that will quickly go over $300 and even $400 psf.
Stick built modern homes can be built to the same specs as these
prefabs for less than these costs in all but the most expensive
areas of the country. For example, in my hometown of Philly
(6th largest city in the US) where labor and material prices are
far from cheap, most of the prefab homes I've seen could be
stick-built for anywhere from $125 - $150 psf.
Prefab manufacturers and resellers will tell you that prefab is
cheaper because of the time and labor savings, but let's list
the key factors that actually make prefab more expensive than
site built:
- Manufacturing Facility Overhead
- Prefab manufacturers work in buildings with support staff
above and beyond those actually building the houses. They
also have facility costs such as equipment, utilities and
maintenance ... Site built homes, built by most residential
builders, don't have any of these.
- Manufacturing Company Profit -
These manufacturers are making at least as much profit as
the average general contractor and often more. The majority
of cost savings resulting from the prefab manufacturing
process stays in the pockets of the manufacturer.
- Delivery, Setting, and Crane Fees
- These can easily run $10K per house (cranes aren't
cheap) and can be significantly more if the distance from
manufacturer to site is large. Most manufacturers also
dictate who the labor crew will be, and often they won't be
the best value available.
- Architect or Reseller Fees -
In some cases the fees charged by the architect providing
the prefab can run as high as $30,000 or more. Even in
cases where no additional site customization or design work
is needed, a substantial fee will still be added by the
architect or reseller.
Less Waste. Since prefab is built in a factory they claim
to create much less waste by setting aside their scrap and
reusing it in other projects. What they do not often advertise
is that their structures use 20% - 30% more raw materials than
stick-built homes in order to withstand transportation. That's
no small figure in my book, especially considering that even if
there is waste on-site with stick-built homes you can now easily
hire a waste removal company that will recycle 90%+ of your
construction waste.
There is something called "value engineering" which can be done
effectively on site-built homes and the polar opposite called
"over-engineering" that is often done with prefabs. Guess which
produces more waste and costs the client more money.
One last point on the waste topic. Things like doors swing and
cause damage during shipping so there is a lot of extra bracing
in the house to prevent this damage. On top of that, there are
extra structural supports inside stairwells and such that are
left in the home after delivery. Loose materials to finish the
homes are also left inside the boxes upon delivery. I recently
walked through a delivered prefab with the owner and he offered
me pallets of free OSB because he had so much extra and had no
idea what he was going to do with it. I'm sure every prefab
company is not this sloppy, but it is another indication of
waste in an industry claiming extreme efficiency.
Less Time. Most prefab companies will claim that there
are significant savings because the construction process is much
faster than a traditionally built home. The site work can be
done while the home is being built in the factory and the actual
physical build time on the manufacturing floor is only a few
short weeks. However, in practice there may be months before
that process, and months after, that greatly lengthen the time
before the home is ready to be lived in. If you scour a prefab
company's FAQ's, call them or ask others that have gone through
the process you will find that 6-12 months or more is not
uncommon from start to finish. With site-built homes often
going up in 4-5 months where is the time savings in prefab?
More Green. We'll throw this in here because "green" is
hot now, so the prefab companies are jumping in and claiming
superiority again in the green realm. Much of the green claims
in prefab come from the lower waste myth that was dispelled
earlier. The new one that we've been hearing more of lately is
that the insulation is installed to better standards than
site-built homes because of the superior labor and inspections
put in place by the factories.
This seems like a weak claim for a number of reasons. Most
prefab companies are still using loose, batt insulation that is
often falling out of the framing by the time the modules reach
the site. Batt insulation alone is not what is making the
better green homes out there more energy efficient. Also, in
many cases, all of that house wrap that is supposed to be
sealing up the home from the outside is tearing apart and
falling off of the exterior by the time the modules reach their
final resting spot. Lastly, the extra framing we spoke about
earlier is causing more thermal bridges in the building
envelope. In other words, the more structural framing that
connects to both the drywall inside and the exterior sheathing
outside, the poorer the total insulation of the home. Wood is a
very poor insulator.
A Possible Hybrid Prefab and
Site-Built Approach
What if you were to take the
best of both prefab and site-built methods of home building and
combine them into a hybrid approach to construction and home
delivery?
First, let's start by roughly defining what this hybrid method
might include:
- Quality, stock plans from qualified
architects that meet local codes and can quickly receive
zoning and building permit approvals.
- Educated clients that understand they
are not buying a fully custom home.
- Prefab building envelope - SIPs,
ICF's & Precast Walls.
- Internal prefab components made in
local shops -- interior framing, framing with electrical &
plumbing, prefab kitchen/bath/utility pods.
- Better scheduling and local
subcontractor cooperation
Quality Stock Plans
The first place to start when trying to streamline and cut
costs from any building project is with
high-quality building plans from qualified architects. If
every detail down to the last sheet of drywall and bucket of
paint is nailed down and proven out in each set of plans, it
becomes much easier for a GC to provide the best price from his
crew and any subcontractors that are hired for the job. This
can not be undervalued, since any uncertainty on the part of
those bidding on the project will instantly up the quotes. This
is where prefab gets most of the efficiency gains in their
process, by building exactly the same home over and over. They
know exactly how much material and how much labor goes into each
home plan in their library of options.
Another point to make here is the need for plans to be developed
or easily modified for any location in order to ensure a fast
permitting process. Zoning and building permit acquisition can
add months to a building project, so having a way to expedite
this phase of construction can be a significant cost saver that
should not be overlooked.
An Understanding of Semi-Custom by the Client
One of the big reasons that fully custom homes designed by
architects are expensive is not necessarily related to the
architectural firm's fee. It has more to do with the fact that
the client is choosing exactly what they want in terms of
appliances, layout, and finishes. There is nothing standard
about this process. The GCs that bid on these homes will be
forced to deal with any number of materials or construction
processes, some of which they might be seeing for the first
time. They may not be able to get their normal discounts on
preferred brands and the uncertainty in labor costs will add a
healthy premium to their bids. An experienced GC knows that
there will be many changes during construction on these custom
homes due to the owner changing their mind or inadequate
documentation on the building plans, and they will pad for these
changes in their budget.
What clients must understand in any prefab or hybrid method is
that the more custom changes they try to make, the higher their
costs will be. There is not an abundance of quality prefab or
stock plan options out there, which is one of the reasons
everyone ends up wanting to customize so much. If the stock
plan industry grew, then there would be much more variety to
choose from and less desire to customize. In the end though,
clients will still need to understand the cost to value ratio of
customization. Most customizations will probably add $0.50 (if
any) in value to the home for every $2.00 in extra cost that is
incurred to make that customization.
Prefab Building Envelope
Now that we've covered the planning phases of a lower cost
hybrid home, we can get into the nuts and bolts of the structure
itself. The basis of the hybrid system proposed here is that
prefab is good in the right places and in the right doses.
The best example of this concept is SIPs or
Structurally Insulated Panels. SIPs are wall and roof
panels that are prefabricated in a factory and then delivered on
a flat bed truck to be assembled like legos on the construction
site. The SIPs combine the framing, insulation, and exterior
sheething all into one product. The windows and door openings
of a home can also be cut exactly to size with framing lumber
attached so that they are 100% ready for the windows and doors
to be installed on site once they are in place. The product is
superior to traditional insulation methods in that it offers
higher R-values per inch and an overall tighter home envelope.
There is far less thermal bridging with SIPs and dramatically
less air leaking out of the finished house.
The SIPs will often save slightly on material costs when all
components are added together, especially compared to a full
prefab house that requires up to 30% more lumber to withstand
shipping. The SIPs are also flat-packed, usually on one truck,
which reduces transportation costs compared to prefab which will
require multiple truckloads of modules to the site. SIPs can be
handled by a fork lift or lull on site as well as by hand, which
eliminates the very costly expense of a full-sized crane and
operator at the site (always needed in prefab). The panels will
go up in 3-5 days on a typical home which beats stick building
by a long shot considering that the SIPs include insulation and
sheething.
Similar products to SIPs are precast concrete wall systems like
Superior Walls that include insulation. These walls can
significantly reduce time in the foundation and basement
portions of the build. ICF's or
Insulating Concrete Forms is another alternative to SIPs or
precast walls. These are basically hollow blocks of Styrofoam
insulation that can be linked together quickly and have concrete
poured in the centers to form the finished structure.
Internal Prefabed Systems
The next suggested use of prefab in the hybrid model is not
used very often in the US, but has been used extensively for
years in other parts of the world. Many good framers are able
to prefab most interior walls, stairs, and even some floor
decking off-site to speed up the installation process on-site.
This off-site framing can be done in a local workshop while the
foundation is being set on a home and while the SIPs are being
made in a nearby factory.
The next step in this concept would be to include electrical,
plumbing, and gas line runs in these prefabbed walls to further
reduce construction time on-site. The building codes in the US
make this very tricky, but the
Swedes have been doing this for years with great success.
Lastly, the furthest development of this prefab interior
component idea is to actually prefab entire kitchen, bath,
laundry, closet, and utility assemblies at a local off-site
location. These small modules would not be subject to the
strict structural requirements of larger prefab modules due to
their size and the fact that they would not need to travel on
highways. They could be dropped right into the homes as the
SIPs were going in place that could result in the vast majority
of the home being assembled on site in only two weeks. A good
example of this type of system is the
Copod designed and built by a company in the UK.
Advanced Scheduling and Building Team
Advanced scheduling and building is something that goes hand
in hand with a good stock plan and a client that keeps
customization to a minimum. The successful tract home builders
in the country that are building 80% of the new housing stock
can teach us something about process (but certainly not
architecture) in this step also. They have their build
schedules down to the day.
The way to reduce construction costs on site is to eliminate as
many unnecessary delays in the schedule both with each
subcontractor and in between each sub's work on the site. This
can be done by implementing the following:
- A fully developed stock plan with no
uncertainty for the GC
- A qualified GC or Project Manager
that can make and keep a good budget and schedule
- A qualified GC or Project Manager
that can reduce delays with local code officials and utility
companies to a minimum
- A team of quality subs with 1-2
backup subs in each field
This may sound like common sense to many, but
in many custom and semi-custom homes, all of these factors
rarely fall into place. Many construction sites sit idle for
weeks and even months as delays are experience with specific
subs, in between subs or while waiting for local officials to
inspect work that is completed. These delays must be eliminated
to reduce the on site build schedule from months to weeks on a
hybrid house.
Advantages of a Hybrid Building
Method
What are the potential
advantages of this type of Hybrid method of building?
- Faster - A hybrid approach
could easily reduce the total build time of a home from
start to finish to eight weeks or less if properly executed.
- Less Waste - The use of SIPs
to eliminate most framing waste, less transportation, no
crane requirement and the use of a construction waste
recycling company will result in less overall waste than
than prefab or traditional stick built houses.
- LOCAL Labor - This is a big
difference from prefab which uses remote labor to perform
over 50% of the work. There are SIPs manufacturers all over
the country that make the same products and can enable 100%
of the construction of a hybrid home to use local labor and
contribute to the local economy. In my book, this is a big
advantage over prefab.
- More Energy Efficient - Better
insulation, a tighter envelope and fewer thermal bridges
from excessive framing equals a much more energy efficient
home than any prefab on the market.
- Unlimited Designs from Unlimited
Firms - Architects no longer need to develop a costly
and time consuming relationship with prefab manufacturers or
worry about marketing and selling their designs with the
hybrid approach. Many different plans from many different
architects can be used in the hybrid system anywhere in the
country.
- Cheaper, much Cheaper -
Somehow I almost forgot this key point. Bringing high
quality residential architecture to "the masses" will be
done by some type of hybrid building system like the one
proposed here long before prefab will due to the significant
savings in cost that will actually be passed on to the home
buyer.
To Conclude . . . Finally
There are many amazing things being done in prefab, and if
it weren't for my self-imposed ban on mentioning specific
companies and architects, I could name a bunch that I personally
admire. However, there are also a large number of
misconceptions about the benefits of prefab that need to be
discussed, and this post is simply trying to get that discussion
started. Are there points of dispute here? Certainly. Am I
perfectly correct in everything I have said? Probably not. So,
go to the comments and tell me what you think.
Chad Ludeman is
President of Philadelphia-based
postgreen, a
real estate development firm specializing in modern, green and
affordable buildings in Philadelphia’s urban neighborhoods, and developer of the much talked about 100k House.
|